Heat Resistant Fabric Solutions Projects
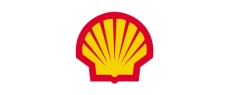
Shell
Platform:
North Everest
Work Scope:
Shell had approached BSV to change-out the full EJ assembly on one of their Ruston turbines
BSV refurbished the old unit, however, due to machine availability Shell wished BSV to install a temporary wrap so that they could utilise the machine in the short-term and re-visit the full change-out of the assembly at a future date.
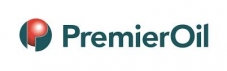
Premier Oil UK Ltd.
Platform:
Balmoral FPV
Work Scope:
Premier Oil asked BSV to manufacture and supply 3 off new expansion joints for one of the Ruston Gas Turbine exhausts plus the supply of new insulation blankets.
Following the removal of flange gaskets with ACM’s (Asbestos Containing Materials) which required the existing duct insulation to be removed BSV were tasked with supplying and fitting new insulation blankets. As part of the exhaust improvements BSV were also asked to change out 3 off fabric expansion joints which had blown and as a result were compounding high temperature issues within the turbine hall.
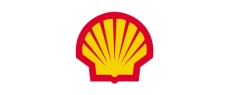
Shell
Platform:
Brent Bravo
Work Scope:
Exhaust silencer for a fire pump had large circumferential cracks on it, however, they had to run the machine and could not remove the silencer due to multiple obstacles in the way.
BSV offered a temporary wrap solution that could be insulated over once wrap in place.
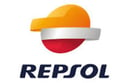
Repsol Sinopec
Platform:
Repsol Sinopec
Work Scope:
Repsol Sinpoec approached us to come up with a solution to multiple cracks and holes in their diesel engine exhausts. BSV supplied a series of high temperature wraps and fitted them with steel banding to secure them in place.
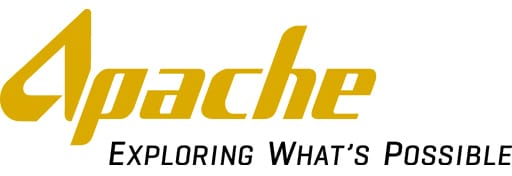
Apache
Platform:
Beryl Bravo
Work Scope:
BSV supplied and fitted high temperature wraps to act as a temporary fixed until such times the expansion joint could be changed out permanently.
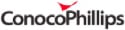
Conoco Phillips
Platform:
Judy
Work Scope:
BSV supplied and fitted new insulation, and repaired existing insulation, just above the newly fitted exhaust expansion joint.
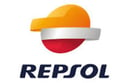
Repsol Sinopec
Platform:
Tartan
Work Scope:
BSV were requested to provide a cheaper alternative to the traditional lagging and tinwork on turbines exhausts.
BSV surveyed and designed a two-layer jacketing system. The primary benefit of this system was the speed of installation where it could easily be fitted in a fraction of the time than that of traditional lagging – saving valuable time and money.
First exhaust that was completed was one of the compressor exhausts, following the success of this we were asked to complete a similar exercise on two of the MG exhausts and WHRU units